Recycling reimagined
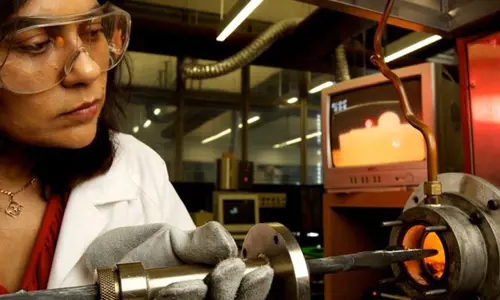
Growing up in India, Professor Veena Sahajwalla was surrounded by huge amounts of domestic and industrial waste from an early age.
That childhood experience sparked a passion for creating value from the things people throw away and set her on a path that has seen her revolutionise the treatment of waste.
“As a young girl I was fascinated by the slum dwellers hunting through landfills for items to sell onto scrap dealers,” recalls Veena. “These people were showing so much initiative by forging a living from what others had thrown out, and I found that incredibly inspiring. I felt there must be a better solution based on those same entrepreneurial principles. So I set out to find it.”
After completing a degree in engineering in India – the only woman on the course – Veena moved to the USA, adding a masters and a doctorate in material sciences and engineering.
“The more I travelled, the more I saw waste was a global problem. I realised the real challenge lay with the sheer volume being sent to landfill because it was made up of different materials that couldn’t easily be recycled.”
But where others saw a problem, Veena saw an opportunity.
“I could see that we needed to change the conversation and start asking different questions. Not ‘will this fit into our established processes for recycling?’, but rather ‘what is this made of and can we use those materials to create anything else?’ If the answer to that second question is yes, then it becomes about how to extract those materials.”
“This wasn’t something we engineers could solve on our own – it needed collaboration with chemists, physicists and the manufacturing industry. I knew the University of New South Wales (UNSW) valued that kind of collaboration, and I felt it was the ideal place to progress my research.”
That collaborative spirit has been integral to Veena’s work since she arrived in Australia. “Ultimately, every idea starts with a simple conversation,” she says.
The BESydney Global Ambassador also acknowledges that while she still approaches projects with an engineer’s mentality, she now spends a lot more time “doing the science.”
The eureka moment
Veena’s first major success at UNSW was her discovery that the carbon and hydrogen contained in plastics could be used to make ‘green steel’, and replace the coke and carbon used in traditional manufacturing processes. It won her the 2005 Eureka Prize for Scientific Research.
She laughs as she recalls the day her team proved it could work. “It was this incredible moment to see a thought experiment I had kept in my head for so long come to fruition. The team kept telling me it worked, but I drove them mad by getting them to repeat it time after time!”
On the back of this success, Veena was appointed Founding Director of UNSW’s Sustainable Materials Research and Technology (SMaRT) Centre, established in 2008.
As Veena and her team further developed the technology behind green steel, they discovered that carbon could also be extracted from end-of-life tyres. They partnered with One Steel (now SIMEC Mining), who rolled it out across their global operations, and together they have saved millions of tyres from going to landfill.
More awards and recognition followed, including an Australian Research Council Laureate Fellowship, and funding for new research into the growing problem of electronic waste (e-waste) – which is now generated three times faster than any other type of waste in Australia.
A small solution to a big problem
Around 600,000 tonnes of e-waste (mobile phones, tablets, etc.) is generated every year in Australia. Globally, the number was 57.4 million metric tonnes in 2021 and it continues to rise.
While the problem is huge, Veena’s solution was anything but. Launched in 2018, her ‘microfactory’ fits into an area of just 50 square metres.
“E-waste actually contains valuable source materials, including gold, silver, platinum and palladium,” explains Veena. “The problem has always been how to extract them. With our microfactory we have a safe, practical and easily scalable solution.”
The microfactory uses a series of patented processes to breakdown and extract the materials in the circuit boards. Highly intelligent precision drones are used to identify target metals within the boards, which are then placed into a small furnace where the identified metals are extracted at different temperatures.
“What’s really exciting is that while eliminating the waste, we are also creating the building blocks for high-performance materials. From discarded phones comes valuable metal alloys that can be sold for a profit, while glass and plastic casings are broken down into silicon carbide that can be used for high-quality ceramics."
The word Veena uses to describe this is ‘microrecycling’. “It’s not chemistry or manufacturing in the traditional sense, but combines elements of both. We are taking complex products back to a molecular level and then rebuilding them.”
After the successful partnership with One Steel, Veena has talked to other manufacturers about leasing this new technology and developing their own microfactories. There has been no shortage of interest, with many seeing potential for their businesses.
Elsewhere, the microfactories are getting attention from media, government and of course Veena’s own peers. “I even had a bank ask me to show them around,” she says. “Which I hadn’t expected!”
The Australian Academy of Science has also recognised the importance of Veena’s work, appointing her a Fellow in 2018. Something she describes as, “a wonderful surprise and such a huge honour.”
Changing mindsets
Looking to the future, Veena believes the microfactory concept could completely change how we think about and treat end-of-life products.
“Imagine if we reached a point where everyone was taking their waste to their local microfactory and coming away with something made from that waste. It could be a gift for a friend or something practical for their own house.”
“The local council wouldn’t even need to organise time-consuming collection services, because the public themselves would become the transport system. It’s completely self-sustaining.”
She believes Australia has the right culture, and that the appetite is there. “If we build it, they will come!”
“It just needs a mindset shift,” she says. “We need to start seeing the value of waste, rather than simply disposing of it in a yellow bin because that’s what we’ve been told we should do.”
Back to where it all began
The microfactories are also taking Veena back to the very beginning of her journey, and the place that first inspired her passion for creating value from waste.
“There is a lot of interest from India. And in many ways it’s a natural home for the microfactories. There are so many scrap collectors looking for valuable waste, it would just be a case of training and employing them to bring what they recover to the factories.
“The social impact could be enormous because there is such a huge gulf between the 'haves' and the 'have nots'. Through a model of shared ownership, microfactories can help close that gap and start to create a more equitable society.”
So the young girl who grew up watching the slum dwellers was right – there was a better solution. And after a journey that has taken her around the world, it looks like she may well have found it in Sydney.
Professor Veena Sahajwalla is Director of the Sustainable Materials Research and Technology (SMaRT) Centre, UNSW.
More on UNSW’s Sustainable Materials Research and Technology (SMaRT) Centre - http://smart.unsw.edu.au